Energy conservation continues to be a nationwide priority of a country as well as the rest of the world. Tube lights are probably the most extensively used lighting equipment in the modern world. Fluorescent lighting tubes are widely used in a large variety of lighting systems due to their advantages such as longer life time and better luminous efficiency when compared with incandescent lamps. Fluorescent lamps tend to be more durable, economical and efficient than incandescent lamps, wherein most of the electric power generates heat instead of light. Fluorescent tubes are low-pressure mercury discharge lamps in which the inner surface of the tube is coated with a fluorescent material. The structure of a fluorescent tube is not rocket science which has likely contributed to their extensive application for several decades. Despite their positive aspects over incandescent light bulbs, fluorescent lamps have a couple of problems. Fluorescent lights are not efficient and may involve huge amounts of electrical energy to produce light. This is a problem, since large buildings could have a large number of fluorescent light fixtures that remain on for long durations, resulting in a significant waste in energy. The conventional fluorescent tubes have life cycles significantly limited and generally lasting from 3,000 hours to 4,000 hours, and have fairly low power factors, ending up with the issue of relatively high power consumption.
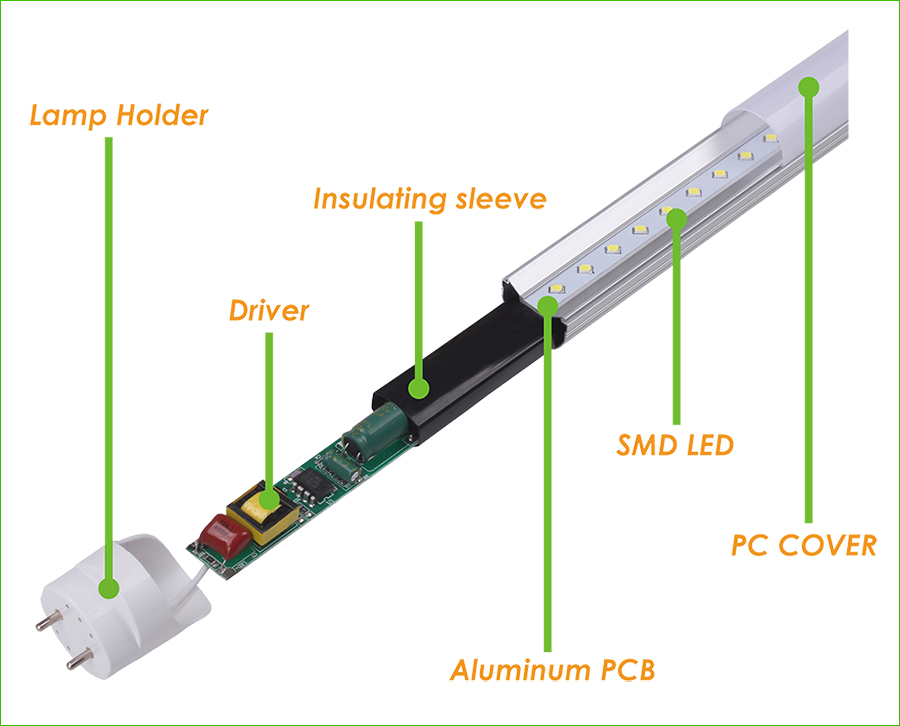
In the continuous effort to bring down power consumption, it is highly desirable to replace conventional light tubes with higher efficiency and more environmental friendly alternatives. Lighting industry and academia devote their time and effort to grow lighting applications with Light emitting diodes (LEDs) due to the benefits associated with this type of solid stating light source in high efficiency, low power consumption, high reliability, fast response time and minimal failure rate. Light emitting diodes (LEDs) are semiconductor light emitting devices effective at generating various colors of light through the recombination of electrons and holes at junctions between first and second conductivity-type semiconductor layers whenever a current is applied thereto. LEDs emit more lumens per watt as compared to incandescent light bulbs and most fluorescent tubes. LED lighting efficiency is not impacted by shape and size, far apart from fluorescent light bulbs or tubes. LEDs can be utilized that emit light of a desired color without resorting to the filters that incandescent or fluorescent lighting would involve to attain the same effect. LED lamps have a considerably longer life than fluorescent lamps and do not contain the hazardous chemicals that fluorescent lights rely upon for their fluorescence. LED lamps at the moment are widely accepted as a more efficient and environmental friendly light source than fluorescent lamps.
Existing linear fluorescent lighting fixtures make use of tube lamping jointly with a ballast and reflector to provide a lighting solution. The fluorescent lamp is run by making electricity to pass through the fluorescent tube via the bi-pins from one end to another end of the tube. The fluorescent tube is operable irrespective of the orientation of the tube when the tube is inserted into the sockets of tube holders. Each fluorescent lamp includes a ballast installed on a fluorescent lamp holder. The ballast converts an external power into a high-frequency and high-voltage power to illuminate a fluorescent tube and continuously delivers a stable current to the fluorescent tube after the fluorescent tube is illuminated. Fluorescent tubes are manufactured in several lengths and styles (T5, T8, T12, etc.). Because of the limitation caused from the shorter lifespan of fluorescent tubes, the design goal of linear lighting fixtures has been to utilize a standardized connection interface, such as the G13 socket, that aids the installation and uninstallation of the fluorescent tube into and out of the fixture.
LED lights are different from conventional fluorescent lights in structural and circuit design. LED tubes are self-contained light engines comprising LED light sources, a driver, thermal management components and lensing. These tubes are designed to match the form factor of existing fluorescent tube styles and sizes (i.e., T5, T8, T12, etc.). Fluorescent lamps are fundamentally driven by electronic ballasts. LEDs alternatively are low voltage direct current (DC) devices. LED tubes do not accept the voltage output of the old fluorescent ballast. The tubes require the fixture to be re-wired, in most cases bypassing the ballast and delivering the retrofit tube with the mains voltage. LEDs can effectively be dimmed either by pulse-width modulation or reducing the current to them, while fluorescent lamps involve expensive circuitry to dim, and many use older ballasts that cannot provide dimming in the slightest degree, the ballast requiring a standard (undimmed) input of AC power. Different to other light sources, LEDs designed for visible light illumination radiate almost no heat in the form of IR that can result in damage to sensitive objects or fabrics. Wasted energy is converted to heat via the base of the LED. These operating variations may require replacement of not just simply the fluorescent bulb itself, but also some or all of the other components of the fluorescent lighting fixture. Reduced maintenance costs from the use of LEDs with their extended lifetime, and not just energy savings, is usually the more decisive factor in determining the payback advantage for switching to LED lighting. LEDs are compact in sizes and exceptionally durable as they are solid-state components, which are very difficult to damage with external shock, different from fluorescent and incandescent bulbs, which are fragile.
The purpose of retrofit is to replace a fluorescent tube with a LED tube without the need of changing the lighting fixture structures. In these, the physical dimensions are identical to in straight fluorescent tubes (e.g. T8 with a diameter of 26 mm and a length of 60 or 120 cm), whereby the fluorescent tube could be directly substituted with a LED tube in an existing fluorescent lamp. The ballast used with florescent tubes is not competent at providing the power requirements of the LED tubes and is often removed, disconnected, or deactivated in retrofits. In today's retrofit application of a linear LED tube lamp to replace a preexisting fluorescent tube, consumers may choose either to opt for a ballast-compatible LED tubes with an existing ballast employed to operate the fluorescent tube or to implement an AC mains-operable LED lamp by removing/bypassing the ballast. A power supply/driver is needed to convert the utility power to the suitable power requirements of the LED tubes. The sockets are subsequently wired directly to AC main power lines which includes a power line and a neutral line (i.e., a ground line).
A retrofitted LED tube requires the same, substantially the same, or similar footprint and form factor in order to replace the florescent tube. Inside LED tubes, there's a printed board or a equivalent structure, on which LEDs and electronic current supply components they require are mounted. The objective of these components is to convert the alternating voltage of the mains into direct voltage and to control the direct current needed by the LEDs. The LEDs may be in a series or parallel circuit array. The LED circuit board is commonly enclosed in a housing which include a metallic housing, typically constructed from extruded aluminum, and a transparent plastic housing (polycarbonate or PC). Wherein the tube body is instructed to play a triple role: light directing, circuit board fixing and heat dissipating. The metallic portion of the housing serves as a heat dissipater while the plastic cover shields the LEDs against external environments and diffuses the light emitted from the LEDs. The heat generated by the LED arrays is first transferred to the tube body via the circuit board and dissipated to the air ultimately. Because LED light tube is a replacement of the fluorescent tube, an end cap structure for the LED tube is compatible with an end cap for the fluorescent tube lamp.
The tube bodies of the existing LED tubes could be categorized into two types: one is made of full plastic tube. Another one includes a plastic tube and an additional aluminum heat sink mounted on the back side of the tube. Under such a circumstance, for the first type of LED tube, as the plastic material will soften over time by heat, and in addition influenced by the action of gravity, the middle portion of the tube lights away from two ends of the tube lights isn't able to stand the gravitational force of the tube lights and is therefore bent toward the ground as a consequence of insufficient material strength of the tube lights. The aesthetics and safety of the LED tube are hence impaired. For the second type of the LED tubes, as benefitted from the support by the aluminum heat sink mounted on the back side, aside from the better heat dissipation, the LED tube will not deform easily by heat, and consequently could remain in aesthetic for an extended time and has a more stable fixing. Nonetheless, as using aluminum materials, the manufacturing cost is considerably increased, the emitting angle is reduced and the lighting effect is for that reason impaired as a result of existence of the aluminum heat sinks. The plastic covers for LED tubes are typically polycarbonate or PC which is an ideal housing materials for LED applications, capable of attaining UL 5VA flammability ratings, providing heat resistance and offering excellent processability into complex shapes. Polycarbonate reflective materials can acquire greater than 96 percent reflectivity. Recently nano-plastics are being increasingly used as LED tube diffusers due to their superior properties. There're also glass tubes which do not have the problem of deformation but its market is relatively small since glass LED tubes are fragile. LED tube lights are available in different lengths with both clear and frosted lens styles, in a selection of 3000K, 4000 k or 5000K color temperatures, depending on whether visibly "cool" or "warm" lighting is desired.
Indeed, LED tubes are an appealing potential replacement for traditional fluorescent light tubes. But bear in mind, all LED lighting designers encounter the same typical challenges of heat dissipation, luminous intensity, price point efficiency, product reliability, etc. When it comes to linear LED lighting products, there are two major problems which need to be addressed. One is their optical performance. Contrary to incandescent and fluorescent bulbs, LEDs are directional light sources. That is, LEDs emit light with an intensity that is maximum when viewed on-axis. Currently, LED arrays are mounted in a tube for generating light. As a result of concentrated light emission of LED chips, the light distribution of an LED tube is not as homogeneous and comfortable as that of conventional fluorescent tubes. The light from a conventional LED tube can have a "spotty effect" as a consequence of uneven distribution of light throughout the tube. One other issue is thermal management. The LED tube is very temperature-sensitive. In many instances, the junction temperature of an LED must be kept below 125 deg. Celsius in order to avoid malfunction. This criterion is vital to prevent the LED tube from malfunctioning. In addition, a temperature gradient usually resides along the tube shaft direction of the LED tube. This temperature gradient may cause the LEDs arranged along the tube to demonstrate different lighting characteristics with respect to each other, which produces uneven illumination for the LED tube. The heat generated by LED chips must be dissipated effectively so as to guarantee the optical performance and the operation life of LED tubes.
Although LEDs themselves can operate at least 50,000 hours under a condition of good thermal management for instance when using an efficient heat sink design, the LED driver that operates the LEDs in a linear LED tube generally cannot last so long due to potential failures of a LED driver in which electrolytic capacitors or other electronic components used are prone to fail prematurely, which occurs if high-temperature air builds up around the LED driver. Upon failure, the LED driver has to be replaced. The same lifetime limitation exists in the electronic components employed in the LED light control module. This limitation engenders a new problem unique to the LED luminaire; that is, the LED light source or lamp has a considerably longer lifetime than the driver and the control module.
The electrical circuitry is completely different in an LED tube lights as opposed to in a fluorescent light tube in that the LED tube may provide a current path between the two end caps. Therefore, installation of retrofitted LED tube lights may be a safety hazard. The potential safety problems such as danger of electric shock and fire become especially imperative and need to be well addressed. During installation of a replacement LED tube, an exposed electrical pin poses a risk of shock to a user. If the LED tube implements double-end wiring, when one end of the LED tube connects with the power source, the other end of the LED tube instantaneously becomes live with electricity. Although the LED lamp is turned off and deactivated, the internal electronic circuitry is still live and energizes the exposed pins. As a consequence, the operator will be shocked if the exposed pins are touched. This presents an electrical shock hazard for the installation technician of the LED tube. To eliminate the risk of fire and shock, these regulatory standards establish that there shall halt electrical continuity between the two ends of the tube during the insertion. That is, the two ends of the LED tube must not be electrically connected during the insertion. The LED driver must be mechanically secured in LED tube and electrically isolated to prevent possible electric shock hazards that occur when any one of the wires is accidentally detached from the soldering joint with the exposed conductor in contact with the metallic housing. The electrical current should not energize the LED tube prior to it being completely installed in bi-pin sockets of the fixture.
Yet another concern associated with replacing fluorescent lamps is that each type of fluorescent lamp is equipped with different electronic ballasts to properly start and operate the lamp. Today you will find a huge selection of different types of fluorescent lamps including different types of ballasts in the marketplace, which requires ballast manufacturers to keep an expansive inventory of ballast types. The aforementioned disadvantages drastically limit the replacement of fluorescent lamps with LED tubes within existing lamp fixtures. Hence, there remains a demand for a consumer friendly design and solution to conveniently replacing fluorescent lamps with LED lamps into existing fixtures without the need of modifications, yet adhering to regulatory requirements. There also remains a need for a system and technique for providing a replacement LED lamp that will work with various types of fluorescent ballast systems.
Furthermore, as LED technologies and standards continue to improve rapidly, requirements of an LED luminous efficacy of 100 lumens per watt and a color rendering index (CRI) of 80 today will be unacceptable tomorrow to consumers and the Energy Star program. Similarly for LED drivers, requirements of a power factor of 0.9, a total harmonic distortion (THD) less than 20%, and a power consumption of 20W today may not be satisfactory tomorrow for energy firms to offer energy rebates, a great incentive for consumers and organizations to retrofit LED lamps. Then again, price competition continues to be intense on the market; manufacturers are endeavoring to produce such LED tube lamps at the lowest cost, which is a critical element to be concern to address the above challenge.